Cavity preservation through flood waxing by example of Volkswagen Golf
Cavity preservation is a very important step in the production of a car. It protects the car body against external factors leading to damage and corrosion.
E-Coating alone, oftentimes, does not reach all areas resulting in undercoating. Also, the consequent baking process might see the ovens not achieving the desired temperatures in the cavities. It often happens that these areas are exposed by undercoating, and hence undermining the quality of corrosion protection. This reduces the cavity resistance especially during unfavorable conditions with rain, snow and salt.
To ensure a good quality of corrosion protection within cavities, car manufacturers apply wax coating. The car body goes through the preheat-oven. Then it moves on to the so-called wax-skid. Through holes of the cavity, hot wax is filled in. The car body then moves further, and the wax is drained off.
This process aims to cover all problematic areas ensuring higher resistance in cavities. However, the wax is an expensive product. Minimizing the material cost while keeping the quality high is the key here. To gain the needed corrosion protection, an optimal wax thickness, which is not too high or too low is required. If the thickness of the wax is too high, the corrosion protection breaks. Thus, it is crucial to have process control as early as possible.
This was made possible with the help of alsim PAINT SHOP suite with the combination of the Oven and the Flood Waxing modules in the suite.
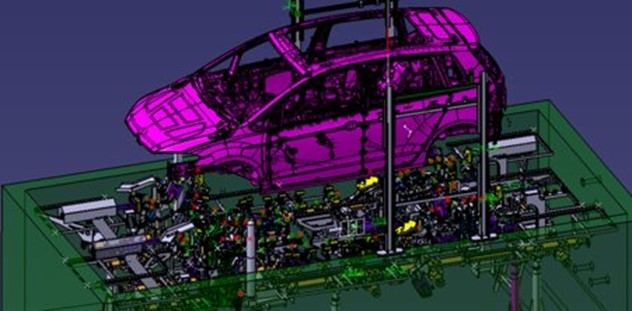
The goals of the project:
The primary goal of the project involved avoiding too high or too low wax thickness, badly waxed regions and residual wax. We wanted to achieve a good wax layer and use as little wax as needed.
The normal process as of today would be as below:
- Waiting for first prototype
- Initially use the same filling and draining settings
- Optimization based on (in cooperation with the vendor):
- Holes in the cavity
- Flow rate
- Filling time per hole
ESS can simulate the heating process in the oven as well as the wax-coating. This can help one save up prototypes to reach zero-prototype status, to optimize the product already in the design phase and to detect problems much earlier.
Volkswagen Group Cavity Preservation Use Case
The Volkswagen Group has become a user of our cavity preservation simulations for preheating ovens and the wax flooding processes. The examples below show simulation results of the flood-wax process and drainage using certain critical sections of the VW Golf. To be precise, the rocker panel of the VW Golf was used in this particular scenario.
To start the simulation, one would normally need to prepare the CAD model for simulation. This process usually takes up lots of time and must be done by experts. Using the alsim platform this process becomes obsolete. alsim MERGE, the pre-processing tool of ESS, automatically prepares the data model for simulation. It can be used by everyone and doesn’t require any special experience or knowledge.
After the mesh preparation is taken care of and before the wax filling happens, the preheating process happening in the oven must heat up the cavity walls of the BIW up to 50-60°C. For this to happen, 100°C hot air is applied. We were able to simulate this with our alsim Oven application to make sure that the required temperature was reached.
The next phase of the process involved the wax flooding. Typically, the total available time for filling process is around 20 seconds. Within this time the injected liquid should reach a certain height inside the cavity to fulfill the process criteria (needed filling height). Optimizing this height was relevant for monetary savings due to the amount of wax being used. The temperature of the injected wax was around 100 ℃ and the air temperature was expected initially to be 60 ℃. Through a database of material temperatures derived from the preheating, correct derived thickness of the wax was determined.
The whole wax skid for the simulation could be set up within minutes in alsim PAINT SHOP by process experts – no CFD experts are needed. The results of the simulation could be seen on the fly. They could also adapt the mass fluid flow duration during the simulation to find the best flow and time conditions to not fill the cavities too high or low with wax.
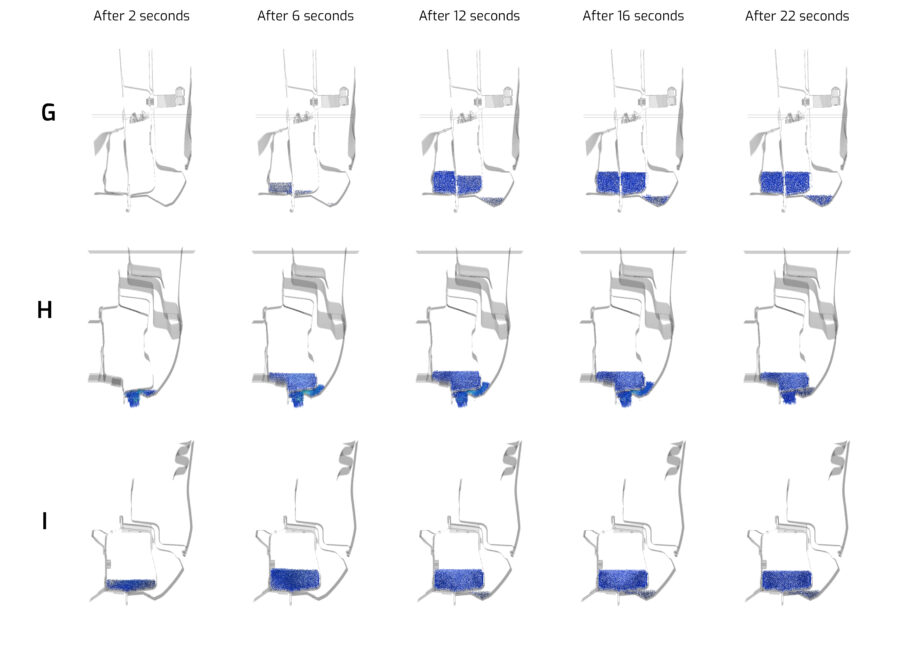
Above, the different filling levels inside different sections of the VW Golf can be seen. After the filling, the wax needs to be drained. Eventual residual wax has to be avoided at this point. We later analyzed the puddles and adapted the design according to the analysis at a later point.
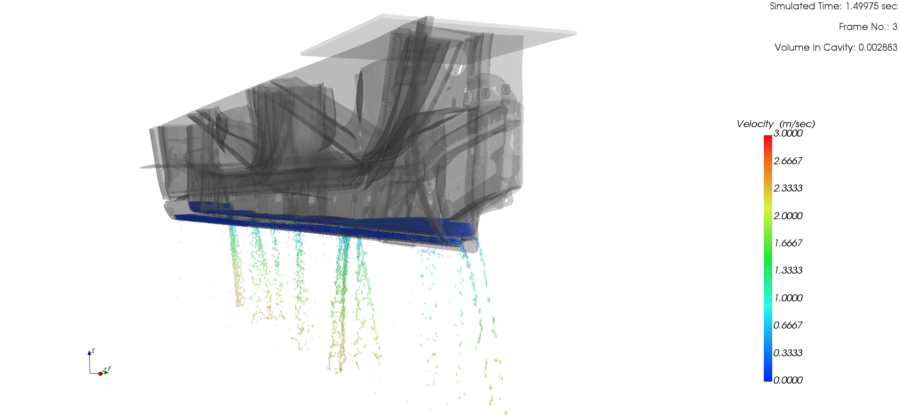