Though the complexity of the processes in automotive paintshop might differ for various manufacturers, the overall paint process persists to be similar. âDip & drainâ is one such method that is practiced by all automotive manufacturers. Conducted as a part of the Electro-coat paint operation (ELPO), this stage essentially helps in depositing a primary anti-corrosive coating of paint.
In the electro-deposition stage, the BIW is given a strong negative electrical charge and immersed in a dip tank of positively charged paint. However, the manner in which the BIW is dipped in the tank and the subsequent drainage after removing from the tank is extremely crucial to the quality of the paint. An inadequate procedure or design can create several problems that thwart the longevity of a manufactured vehicle. For this purpose, appropriate measures are taken by every automotive manufacturer to optimize their dip & drain process for every vehicle design. Corrosion being one of the primary detriments for a vehicle, this stage is crucial for any automotive manufacturer.
Air bubbles (voids) and puddles are two common problems solved through alsim Paint Shop Dip Paint.
Air bubbles appear during the dipping phase whereas the paint puddles appear during the draining phase in a paintshop. Air bubbles are a result of the dipping angle and the movement of the BIW when it goes into the dip tank during the painting process . The air volume trapped on the surface of the BIW hinders the sheet metal from having contact with the e-coat liquid, which leads to sparse or no deposition of paint. The presence of air bubbles can, thus, cause non and badly painted areas. Dip Paint module enables all users to easily determine the problem areas where air bubbles can potentially occur. This allows the manufacturer to improve their design or adapt the paint path to minimize the entrapment of air.
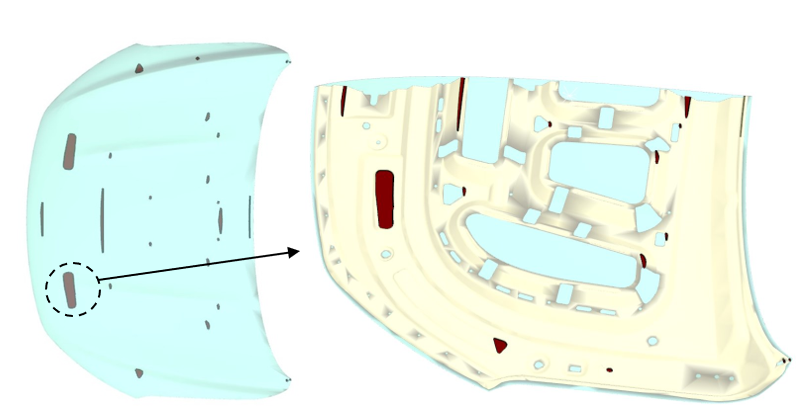
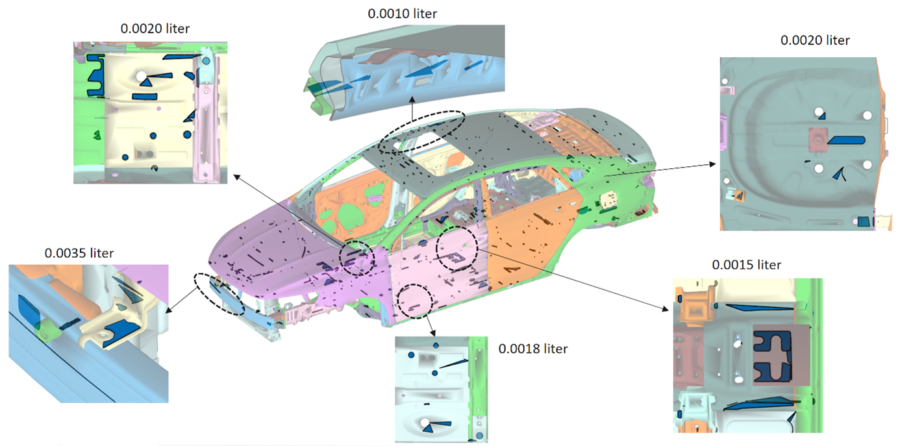
Puddles can occur when the paint liquid stays in a convex surface and does not drain off efficiently. This could create further problems during the baking of the BIW in an oven. During baking, as the curing with high temperature occurs, most of the puddles evaporate. However, some of the puddle liquid does not evaporate. Instead, the liquid in the puddle boils , inflates in volume and can cause drips along the surface or could damage the coating in that region. The puddle area and the bake drip area could invite corrosion if another e-coat is not applied. To rectify this issue, it would be useful to predict the puddle areas and the flow of the bake drips, which can be predicted with our alsim Paint Shop. To impede the formation of bake drips, it would also be useful to determine the regions where puddle formation is expected in a particular scenario. This can also be accurately and quickly computed through the Dip Paint module.
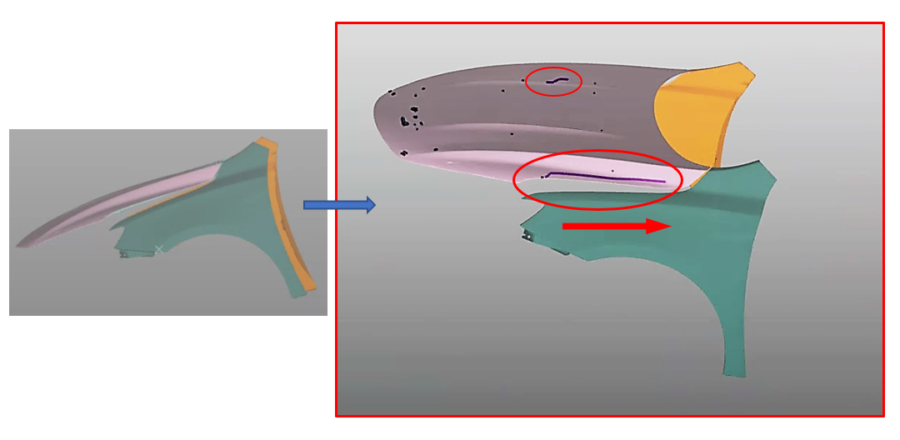
When the BIW is removed from the dip tank, the excess paint material is supposed to drain off, however this is not an immediate activity. The delay can be attributed to the surface tension of the paint material or the BIW. The resulting surplus paint, termed as Retain fluid, can be calculated in Dip Paint module with our new solver computing the real behavior of surface tension and related physics as an upgrade to our recent release. Apart from resulting in a non-uniform coating, the retain liquid is a major wastage of expensive paint material. There have been cases where on an average for a BIW this could even amount to 2 liters of paint!
Of the many parameters that come into play during dip & drain, a key factor taken into account is the hanging position of the BIW and the angles at which its parts are connected. Dip Paint provides a quick option to obtain the optimum hanging position based on the minimum puddle formation for a particular BIW. The convenient option to run a sensitivity analysis provides a graphical representation to determine the most optimum apex angles of the connecting parts, like doors, hoods and lids.
The complexity of the CFD simulation of the dip & drain process is quite high, owing to the huge calculation domain involving tiny elements of interest such as the holes, or the gaps between sheets. The computation techniques followed by Dip Paint, are nothing short of unique. The distinctiveness begins with the underlying methodology of its solver. Reeb Graphs, an important concept in Morse theory, is one such distinctive method used in Dip Paint to gather the topological information. In contrast to the conventional CFD methods, the number of elements used in our computation is drastically reduced, by a scale of at least 100, thereby providing very fast computational technique. This is due to a different mesh representation technique used in our solver, which subsequently reflects in the speed of obtaining the results. Also, the solver is developed with appropriate measures including a topological method allowing the tracking of flow through narrow channels of all sizes thereby ensure highly accurate and efficient results.
For quick identification of problem areas, pertaining to air bubbles & puddles, the provision of âAirbubblesâ approach in the module allows for very fast computation. It is faster than the conventional methods by a factor of 2000. âDrainageâ, being the other approach used in the module, allows for time-dependent simulation. This is useful to obtain results that include drainage time, and to optimize the time taken for each step or the whole process. It is estimated that Drainage approach is around 150 times faster than conventional CFD methods. On an average, it would take 80-90 hours of computation time to simulate the process for a BIW using Drainage.
Conclusion
The module, unparalleled to any other solutions in the CFD market, has been designed in accordance with ESSâs motto and the competitive advantage offered by every solution of ESS. The ease in usability built up through simplified workflows, pre-defined bath, and boundary conditions. Even though dip & drain is performed along with e-coating process in real-world, designing an individual application for dip & drain augments the usability of the module, making it easier for non-CFD experts to run, otherwise complex, simulations. The air bubble results obtained from Dip Paint module can be fed into E-coating module at a later stage, thus satisfying any interdependence.
Prediction of application defects and their movement is extremely important to ensure absolute corrosion protection and consequently, total paint coverage. alsim Paint Shop Dip Paint users would not only be able to ensure superior paint quality but also gain complete process control. From the hanging position of the BIW to the time needed for draining, one will be able to conduct in-depth analysis of its dip & drain process and optimize the process to maximize efficiency. One can curtail both the capital and operational expenses by optimizing paint material usage. For every 100 sqm of vehicle surface area, saving 1¾m of paint accounts to 1⏠saved. To put this in perspective, if one manages to optimize and reduce the excess paint thickness by 10 microns on an average for a car, they can save around 10 euros, and with at least 500 cars manufactured per day, we are talking about savings of 5000⏠daily!