Škoda Auto, one of the leading car manufacturers in the world, has been using alsim Data Cleaning Merge and alsim Paint Shop, the CFD software solutions offered by ESS, to optimize their paintshop process and reduce their environmental footprint
Requirement
- Internalising CFD usage for paint shop
- Refining paint quality and improving efficiency
Key Successes
- In-house usage of CFD
- Identify possible quality issues in advance
- Significant costs reduction
- Quick implementation and training for the team
ESS Solutions
- alsim Data Cleaning Merge
- alsim Paint Shop Dip Paint
- alsim Paint Shop Oven
According to Petr Havlík, a development engineer at Škoda Auto, the software modules have exceeded their expectations and they use it once or twice a week as a part of their regular activities. They found the most useful modules to be alsim Data Cleaning Merge for data preparation and alsim Paint Shop Dip Paint – which provides them insight into the RoDip kinematics process including the estimation of liquid carryover and air bubbles. This not only saves time but also makes their tasks significantly more efficient and flexible.
With alsim Data Cleaning Merge, one body-in-white takes approximately 5 hours. All checks are fully automated such as duplicates, collisions etc. This is a massive improvement.
Software instead of Service
The initial training provided by ESS was efficient, and the GUI and the steps of the process were easier than they thought it would be. “The team of ESS were (and still are) keen to help, always making sure we get what we need,” says Petr. The decision to purchase the software licenses instead of requesting a service project was driven by their need to build their know-how and in-house execution capabilities. This not only saves time but also makes their tasks significantly more efficient and flexible.
Sample geometry of Škoda Karoq representing the ESS solutions used at Škoda
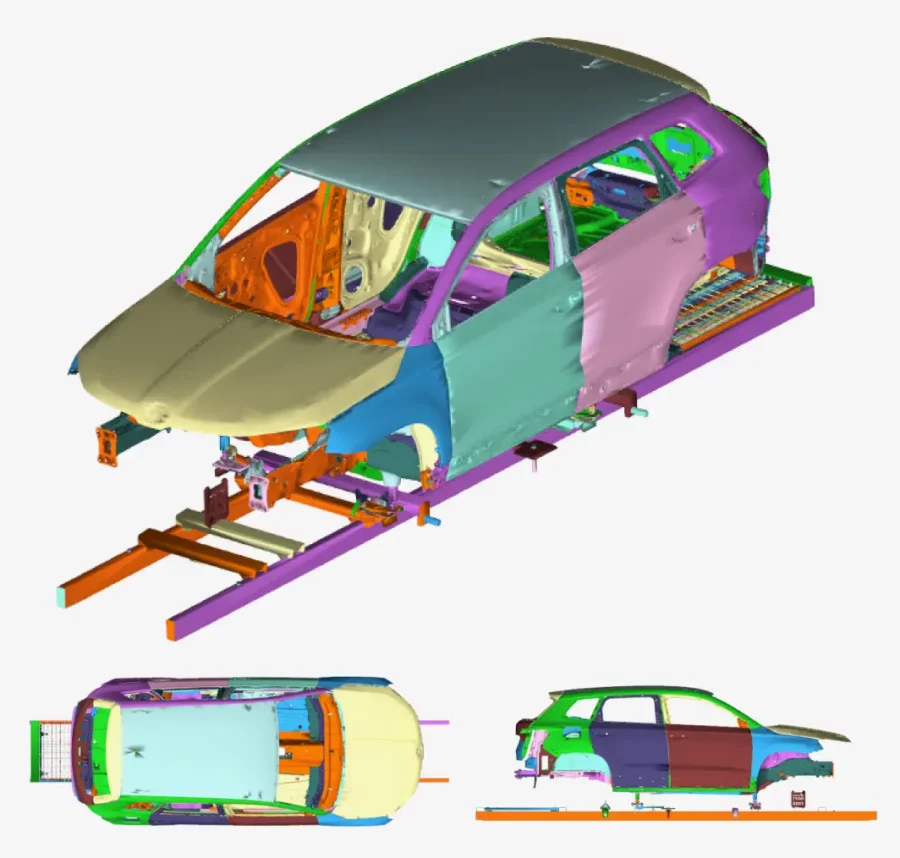
- Air Bubble Simulation
Simulation
In this example the simulation of BIW through paint shop E-coating tank was taken. The animation shows all the Air-Bubbles and Paint Puddles during the complete paint path.
filter settings for Air-Bubbles
- Removed volume smaller than 100 mm3
- Removed height smaller than 1mm
Air-Bubble on the rear underfloor assembly. Total volume: 4.2 ml
Air-Bubble on the rear underfloor assembly. Total volume: 3.9 ml
Air-Bubble on the upper tailgate panel. Total volume: 4 ml
- Paint Puddle Simulation
Simulation
In this example the simulation of BIW through paint shop E-coating tank was taken. In this example the animation shows the major Paint Puddles during the dip-out process.
Total Puddle volume = 10.735 l
Total Puddle volume = 5.323 l
Total Puddle volume = 2.09 l
Graphical results
Observation
- The above graph shows only dip-out process and 60 sec of holding period of BIW in horizontal position.
- First graph shows the variation in Puddle volume (Retained water) on the BIW vs. time. It can be seen that after the holding period of 160 sec, the final Puddle volume left on BIW is around 0.145 liters.
- Second graph shows the liquid drained through the bottlenecks in every time steps.
- Bake Drip Simulation
The presence of excess puddles on the inner panel of tailgate can lead to the formation of bake drips during oven process, which may reduce the quality of the paint.
puddle volume 2ml
Bake drips can be formed on rear floor assembly panel as shown below.
puddle volume 12ml
Bake drips can be formed on rear bumper assembly during oven process as shown below.
puddle volume 1ml
This not only saves time but also makes their tasks significantly more efficient and flexible.
According to Petr, “Data preparation and cleaning is known to be the most hideous processes of all. Now with alsim Data Cleaning Merge, one body-in-white takes approximately 5 hours (depending on the hardware). All checks are fully automated such as duplicates, collisions etc. This is a massive improvement.”
The customization in the modules, such as the definition of a new oven or paint bath, was made easy for the end-users. The easy-to-setup paint bath with different scenarios for multiple paint shops, including pendulum and RoDip kinematics was certainly useful. The alsim Paint Shop Oven module was more time-consuming in comparison, but once the pre-defined oven was completed, it could be reused as many times as needed in the future. With the ESS team on stand-by for additional requests, the custom feature requests from Škoda Auto were delivered in no time
Significant reduction in liquid carry-over from 330 ml to 4 ml, just from the tailgate!
As an example, Petr highlights, “The simulation of the tailgate’s carry-over of a newly developed model showed a significant reduction in the carry-over from 330 ml of liquid to just 4 ml. This simple change could theoretically save Škoda Auto over 50k€ a year. These benefits of using CFD simulations instead of traditional optimization are just the tip of the iceberg, and the impact could be even greater when working on the validation of a whole body-in-white.”
The software’s usability, customization, pre-defined parameters and lightning-fast results have made it an invaluable tool for the company. With ESS solutions, Škoda Auto has been able to take a substantial step towards a greener future and reduce their environmental footprint.
The Results
Before using CFD simulations, the engineers faced problems with saving time and the complexity of project management. The results from the ESS modules helped in saving time and resources, such as personnel, material, and energy consumption. The impressive reporting feature allowed them to generate charts with just a click of a button. This would be further improved with the new Automated Reporting feature being introduced by ESS, which will save a significant amount of time for their engineers in interpreting and analysing the results!