Comparison of tailgate drainage experiment results and alsim Paint Shop simulation results for Audi
Over the years, as the paintshop techniques have evolved, there is a growing realization of the importance of simulating various processes of the paintshop. A virtualization of the process with respect to the paint line and the BIW design being manufactured helps reduce wastage of resources and improve the paint quality. alsim Paint Shop suite provides the perfect set of tools to simulate all the processes currently employed in major paintshops across the world. Filling and Drainage is one such process in the paint line that if simulated accurately can improve the paint quality on the BIW and reduce the wastage of paint materials drastically.
To prove the simulation capabilities of paintshop – specifically with respect to the drainage process – we conducted a validation experiment. This was conducted as per the requirements provided by Audi and was subsequently compared with the results obtained from alsim Paint Shop.    Â
Experiments
The experimental rig that was setup inside the ESS office (See Figure 1) is one of the most striking aspects of our validation process. This was built in a short span of time by our employees without any external help, with utmost care and craftsmanship. The rig has proved to be capable of bearing heavy load with high stability. Since the primary requirement of the rig was to capture the real-world behavior accurately, the structure provides the tailgate the freedom of movement in all three directions. This was crucial for the steps followed in the validation and for the proximity to our simulation results, specifically during the drainage stage.
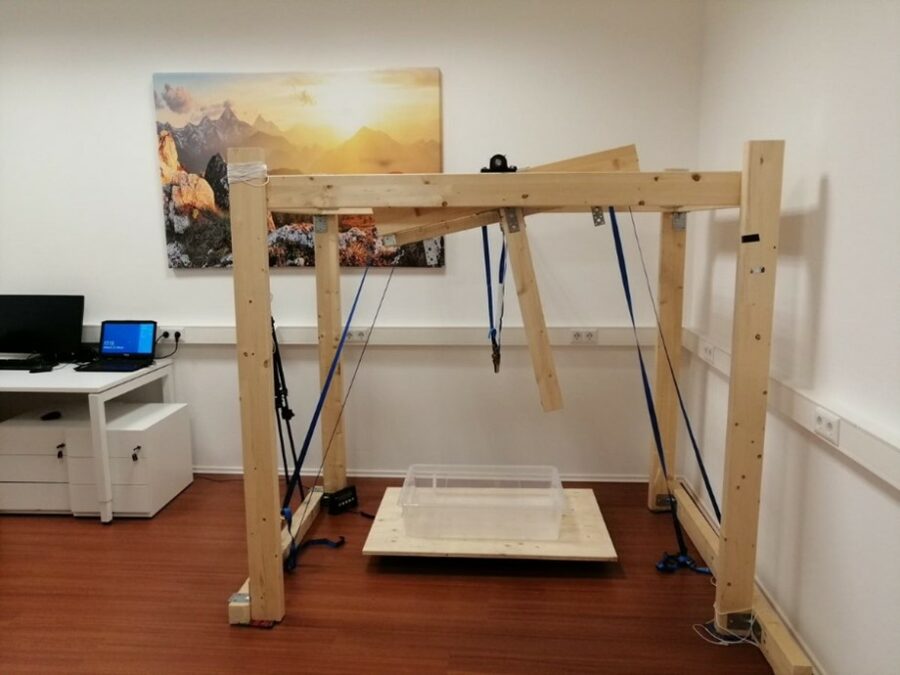
After careful study of the requirements from Audi, the experiment was divided into 6 stages. The holes in the tailgate were categorized into 3 sets of configurations (Figure 2). And each configuration, was further performed in two different hanging positions at 0° (horizontal)​ and 15° (rotated). The rotational capability of the rig was essential to set the tailgate at 15° hanging position.
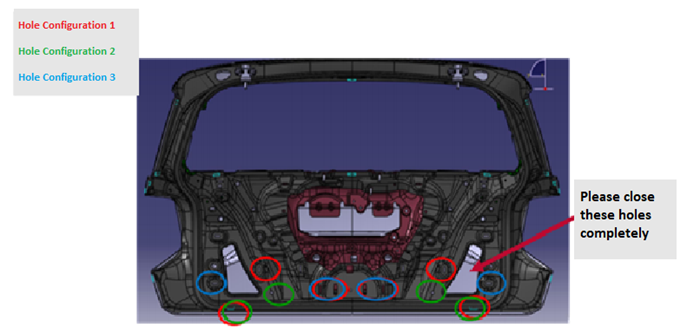
In order to drain water off the tailgate, manual-opening of the tailgate holes would not have fetched accurate results, as the action may not be perfectly simultaneous. For this reason, Interec 100 N 12V/DC electromagnets were used in the experimental setup. (See Figure 3).
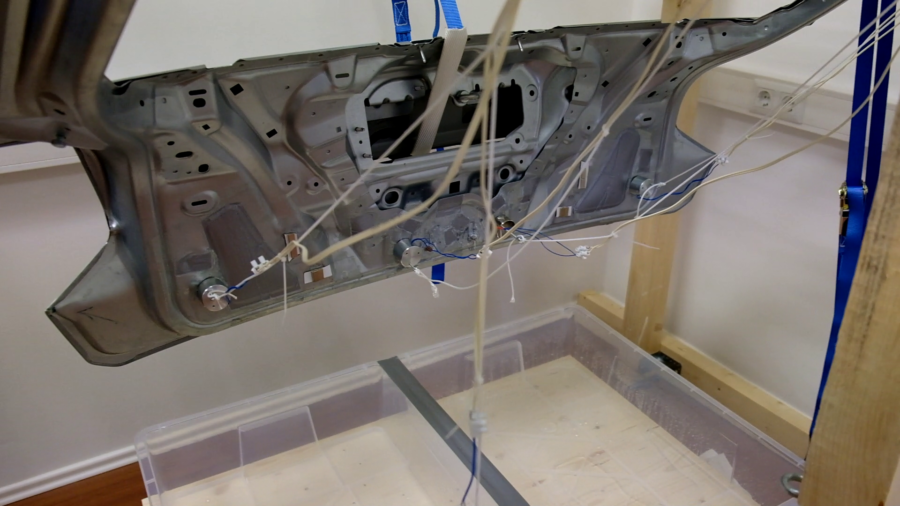
Once the setup was finalized, we began the validation by closing all the holes of the tailgate. An exact volume of water, approximate to the amount used in the simulations, was filled into the tailgate. This fill volume was provided by Audi.
Based on the set of holes for which the experimental stage was conducted, we cut-off the current in certain magnets to open a specific set of holes. The drained-off water from these holes, was caught in a vessel which was automatically measured using a RADWAG PM50 scale with a precision of 0.001kg. The readings were simultaneously captured and stored in a CSV file. This was essential to get the exact readings at every 1/10th of a second in a span of 70-90 seconds for each stage. The results in kilogram were then converted to the volume of water drained. To ensure a realistic and accurate reading, the averages from 3 iterations for each experimental stage were used. These readings were required to compare the results obtained during our simulations.
The next stage was to conduct the experiment for the same set of hole configurations after rotating the tailgate to 15°. Later on, the experiment was repeated for the 2 other hole configurations in a similar manner at two different hanging positions (0° horizontal & 15° rotated). The values received from all the 6 stages were then compared with our simulation results and presented to the team at Audi.
Simulations
alsim Paint Shop v4.1.9.3 was employed for the simulation of the tailgate drainage. The CAD model of the tailgate received from Audi in NASTRAN format was fed into the software. After setting the position of the tailgate and closing the holes, the tailgate was filled. The simulation was conducted after selecting the holes used for drainage. The process on an average, for all the 6 different stages (for 3 hole configurations at 2 different hanging positions), took 15 minutes. The results of the drained volume during the process was exported in CSV format and used for the validation with the experiment. Images from one of the simulations at 15° rotated hanging position can be seen in Figure 4.
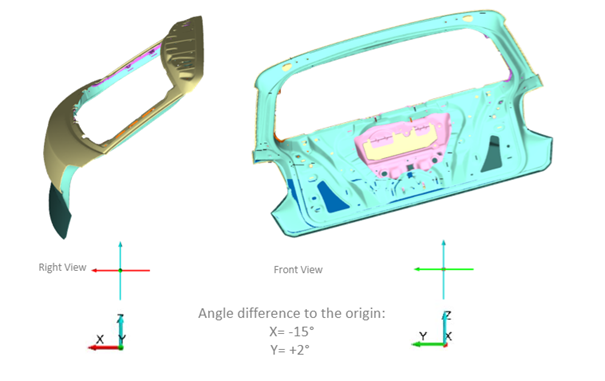
Conclusion
The results from 1 out of the 6 stages is provided below as a reference. Please note that this is not an average of all the stages, but instead the values obtained during one of the stages. As can be seen in the Figure 5 & Figure 7, the volume of water drained from a set of holes in the experiment is precise to the volume drained during our simulation. Another graph was plotted for each stage, which depicts the difference in drained volume over time (See Figure 6 & Figure 8).
0° horizontal hanging position
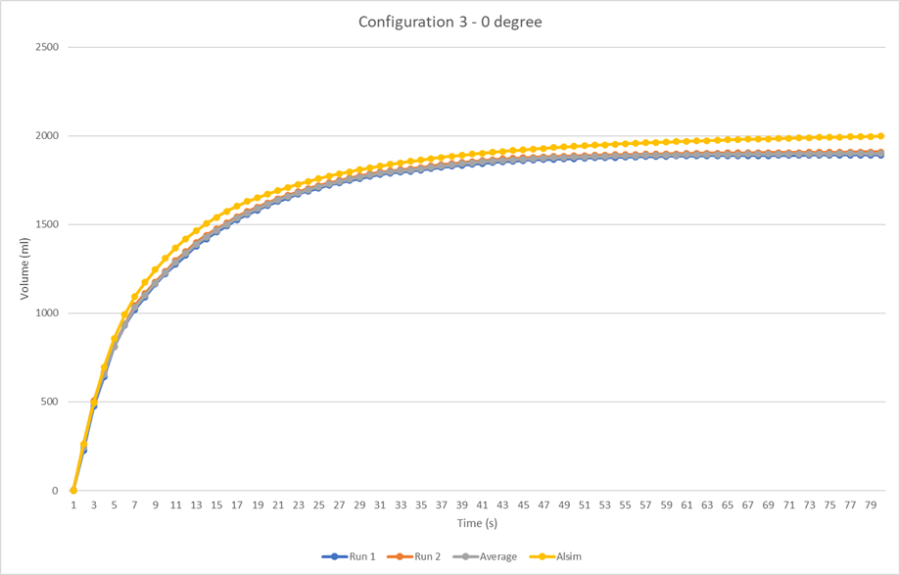
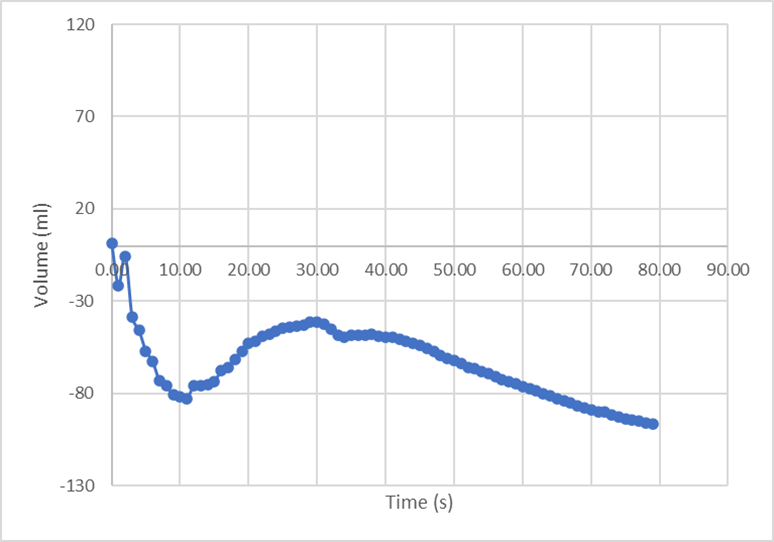
15° rotated hanging position
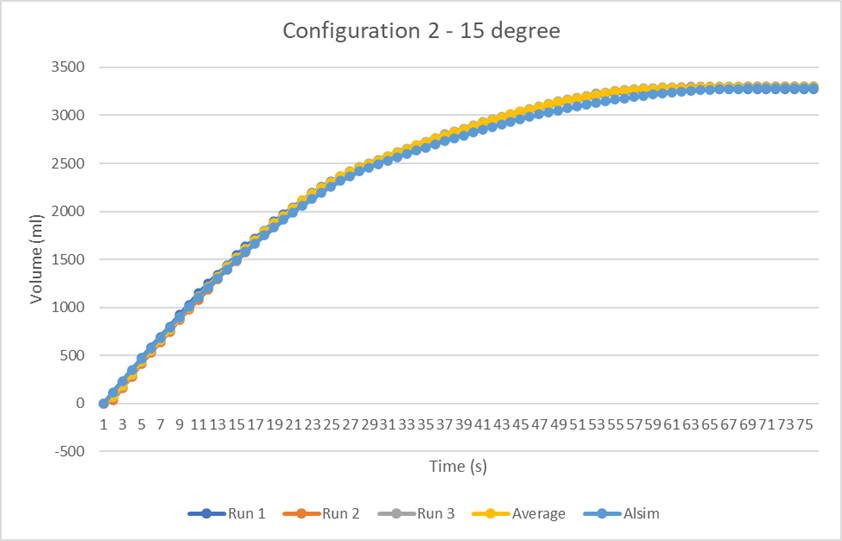
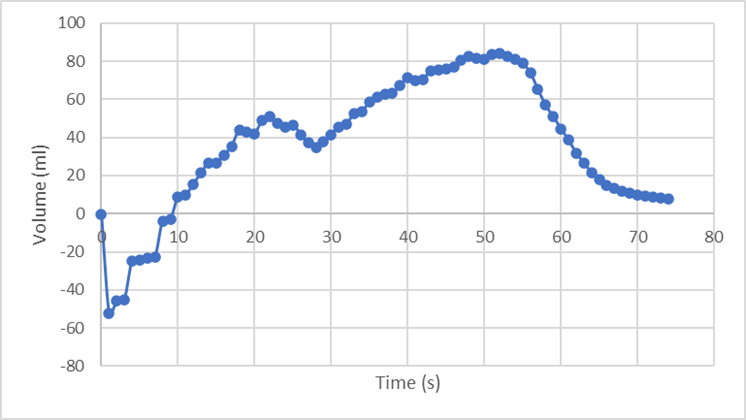
To summarize, our simulation results were extremely close to the results obtained from our validation. The requirement for the drainage volume provided by Audi entailed us to produce a simulation result which does not deviate from the validation experiment by more than 100ml. This requirement was easily met as can be observed from the graphs. Not only is the deviation of drainage volume less than 100 ml, but majority of the values we got at every 1/10th of a second was close to the validation experiment results by not more than 60ml. There can be a slight deviation between the simulation and the experimental result, due to the manufacturing tolerances of the tailgate. This can have a big impact on very small holes as they play an important role during drainage. Generally, a variation of even 5% due to manufacturing tolerance would have caused a bigger impact in the simulation results, considering which the requirement of 100ml was proposed by Audi. But our simulation results easily surpassed this requirement. Thereby, proving that the deviation does not cause any major inaccuracy in our results, and is well within the prescribed standards.
In comparison to the major players in the market, the accuracy of our simulation results to the real-world results is extremely high. The average time taken by all our simulations was 15 minutes, which is exceedingly quick!
Our unique approach involves personalization of our software based on the physical properties and the physics concerning all the major applications employed in paintshop across the globe. This enables our users to get results that are extremely close to reality, as it mirrors the existing behaviors and methods followed in the industry. This further enables our software to save a lot of computation time and provide highly accurate results with the swiftness unbeatable by any other simulation software in the market. The ease of usability being an additional strong point due to the high customization, further proves the competency of alsim PAINT SHOP. To sum up, alsim PAINT SHOP can be used by anyone, from process experts to non-experts, to take full control of their processes/designs by optimizing it within a very short duration.